jvanhees
Well-known member
Figured I would post this up here as a separate topic, as it is important to get all the opinions I can on this...please let me know the best way to fix this oh experienced veterans!!! [-o< This is the joining piece of metal(keel ?) coming down from the front top - joining both sides together in front...If you followed this peice up further, to hook hole for the winch is there. This is a picture of the boat flipped over. sorry for the horrible terminology. I think this is where the PO ran his boat ashore all the time.
The large red circle is the main crack, and will be tig welded. The small red circle is the other crack I found...much smaller but will still need welding. The green circle is to show the that riveted seam..and it leaks alot across the whole seam..even with the junk from the PO.
The blue rectangle shows the main problem area....how would you fix this?
1) Do I weld the 2 cracks, replace each rivet and seal with steeflex over top of it all? Will that be enough?
2) Weld the entire seal where the rivets are now all the way around the rectangle piece of aluminum(edge where marker lines point to), and also replace the rivets inside the welds...then steelflex?
3) Form a new piece of aluminum to go over what is currently there, extend wider by an inch on each side(size of the blue rectangle), and fully weld it in...covering over the entire area with a new peice of metal. Sounds the best...
Need some advise here! :?
The large red circle is the main crack, and will be tig welded. The small red circle is the other crack I found...much smaller but will still need welding. The green circle is to show the that riveted seam..and it leaks alot across the whole seam..even with the junk from the PO.
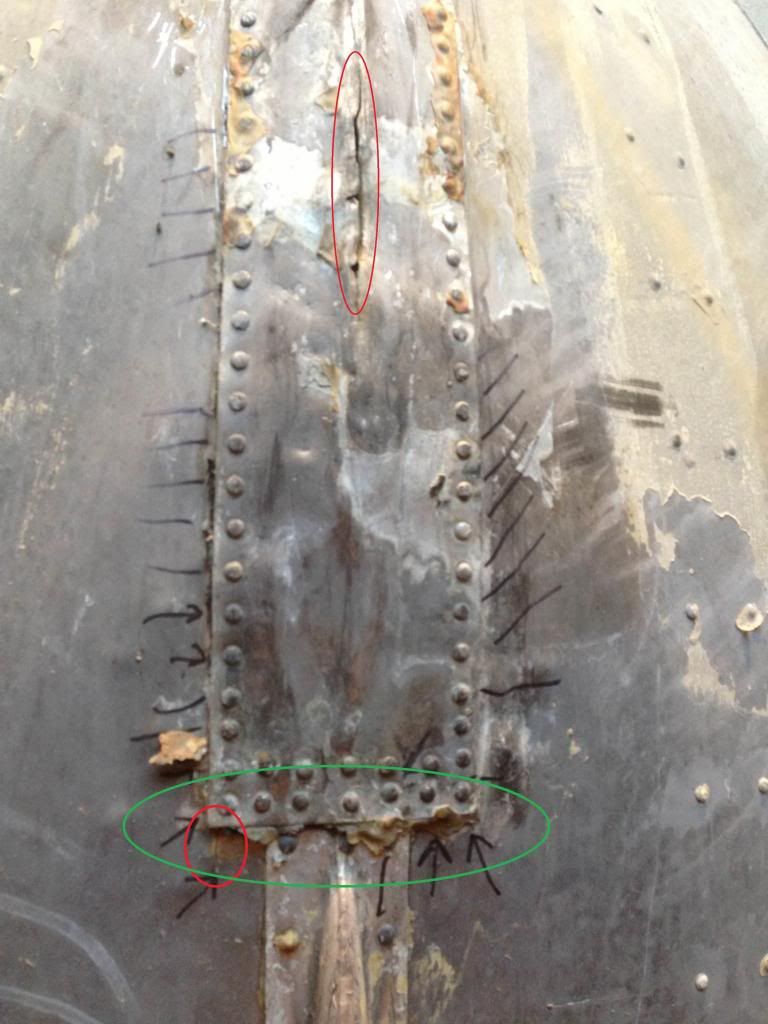
The blue rectangle shows the main problem area....how would you fix this?
1) Do I weld the 2 cracks, replace each rivet and seal with steeflex over top of it all? Will that be enough?
2) Weld the entire seal where the rivets are now all the way around the rectangle piece of aluminum(edge where marker lines point to), and also replace the rivets inside the welds...then steelflex?
3) Form a new piece of aluminum to go over what is currently there, extend wider by an inch on each side(size of the blue rectangle), and fully weld it in...covering over the entire area with a new peice of metal. Sounds the best...
Need some advise here! :?
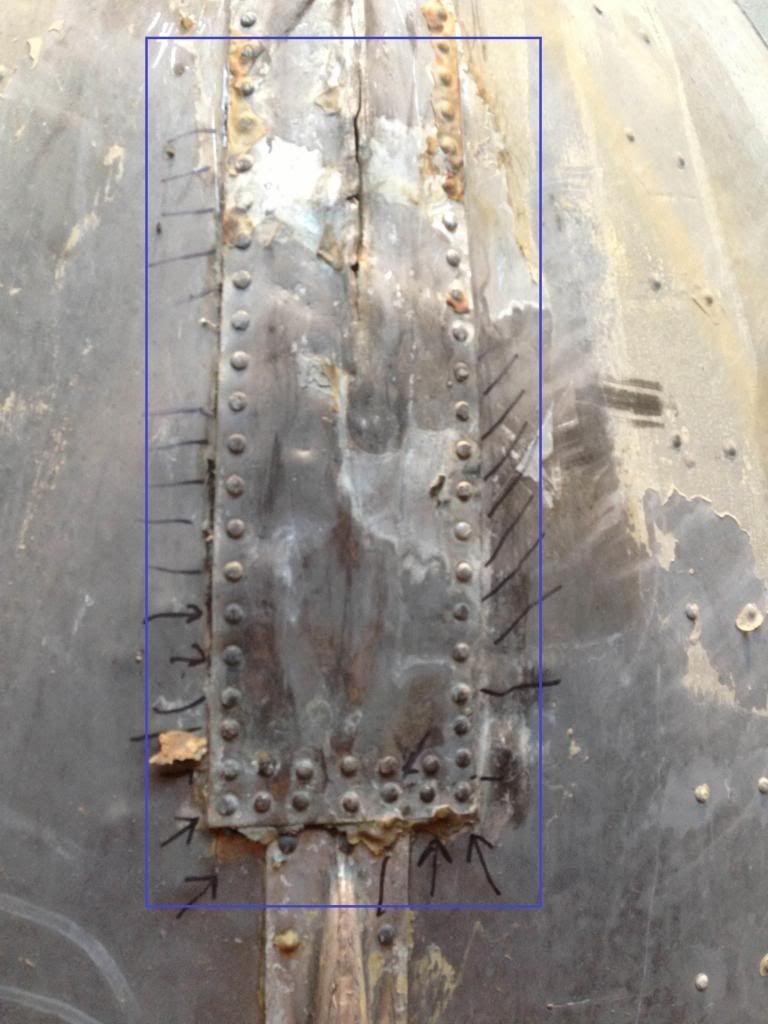