timebak
Active member
When I was buying my present home, back behind it this boat was sitting on a trailer. It had been there so long that the tires were sunk into the ground to the axle and the hitch dolly wheel was completely sunken out of sight in the dirt. Upon my examination, it was obvious this boat had never been used or in the water. I asked the owner about it and he said he bought it at a Waterfowl event down in Arkansas in 2001 and had never used it. Just never got around to it.
I asked him if he would consider selling it to me. We dickered and settled on 700 bucks, as is, trailer and all. It's a SeaArk 1548DK DuckHawk, a heavy duty boat with all welded hull. But it had a 15" transom.
I started shopping for a good outboard and came across a 2001 Suzuki DF30 30hp long shaft, with power trim and tilt, and electric start, built for remote control, but had no controls with it. It was a display model out of a dealership up in Wisconsin and had virtually zero hours on it, but they were getting rid of it because that model had been discontinued. I struck a deal for $1600 after a thorough inspection of it.
First modification: Build up the transom to 20". Those aluminum plates laying on the back seat are my doubler, or reinforcing plates for where I'm going to install pedestal seats.
I found a great deal on a tiller steering kit at the local Suzuki O/B dealer, and installed it myself and modified the wiring harness so everything will work great with tiller steering. I mounted the motor myself.
More pictures to follow.
I asked him if he would consider selling it to me. We dickered and settled on 700 bucks, as is, trailer and all. It's a SeaArk 1548DK DuckHawk, a heavy duty boat with all welded hull. But it had a 15" transom.
I started shopping for a good outboard and came across a 2001 Suzuki DF30 30hp long shaft, with power trim and tilt, and electric start, built for remote control, but had no controls with it. It was a display model out of a dealership up in Wisconsin and had virtually zero hours on it, but they were getting rid of it because that model had been discontinued. I struck a deal for $1600 after a thorough inspection of it.
First modification: Build up the transom to 20". Those aluminum plates laying on the back seat are my doubler, or reinforcing plates for where I'm going to install pedestal seats.
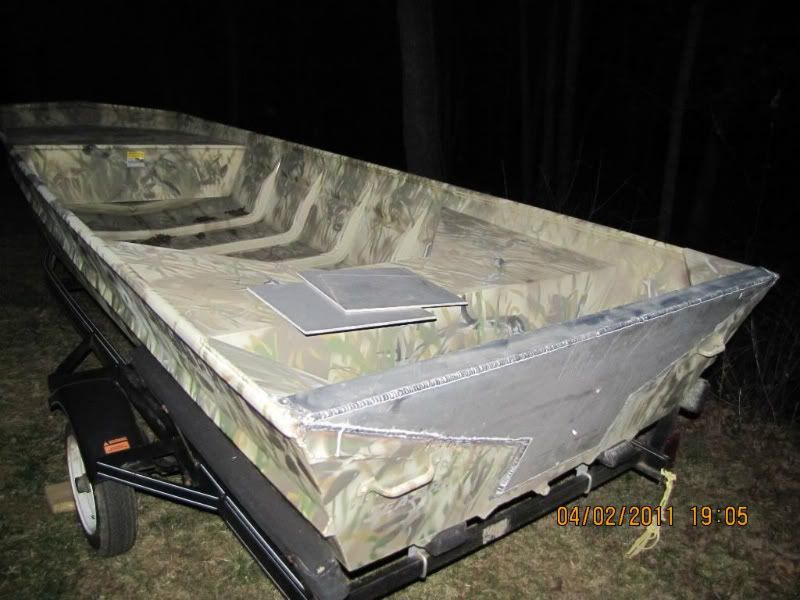
I found a great deal on a tiller steering kit at the local Suzuki O/B dealer, and installed it myself and modified the wiring harness so everything will work great with tiller steering. I mounted the motor myself.
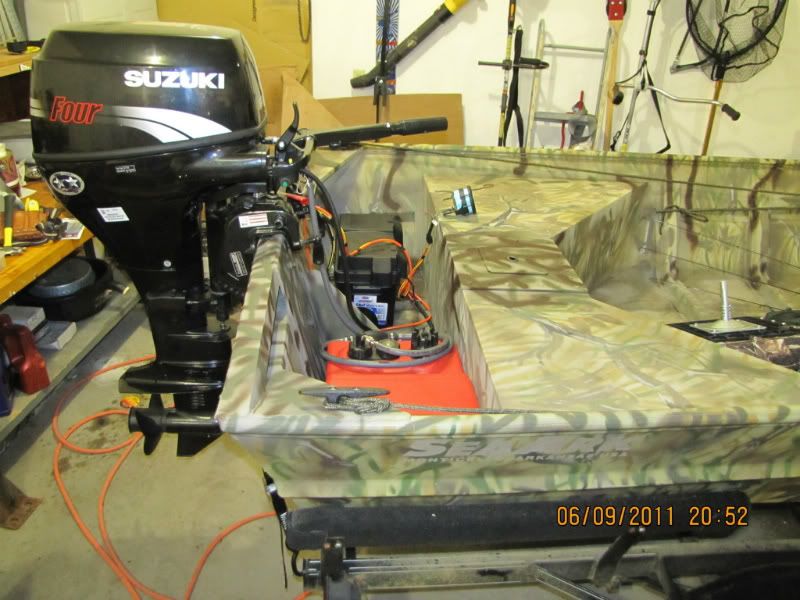
More pictures to follow.