cody0707
Member
I just picked up a 2008 SeaArk. It was used in freshwater but unfortunately, the south's ******* community got ahold of it. There are numerous very small screw holes in the top of the boat. What is the easiest way for a non-welder to fix these holes and apply a rattle can paint job over the repair?
Also one of the previous owners decided to cut access under the front deck and remove foam to allow for storage. While I don't mind having storage I think it was done poorly. I plan to find a hatch to fit in this location and will likely build a box to fit in the hatch then put some foam back around the box. Any recommendation on this plan?
Also, the boat needs a 15" shaft but they have a 20" on it with a jack plate. The jack plate does get the motor to the correct height but it sets the motor back making the tiller reach shorter. A simple tiller extension should fix this issue. I was thinking about putting a grab handle in to allow me to stand up while running.
Here are the photos of their crafty work:
Also one of the previous owners decided to cut access under the front deck and remove foam to allow for storage. While I don't mind having storage I think it was done poorly. I plan to find a hatch to fit in this location and will likely build a box to fit in the hatch then put some foam back around the box. Any recommendation on this plan?
Also, the boat needs a 15" shaft but they have a 20" on it with a jack plate. The jack plate does get the motor to the correct height but it sets the motor back making the tiller reach shorter. A simple tiller extension should fix this issue. I was thinking about putting a grab handle in to allow me to stand up while running.
Here are the photos of their crafty work:
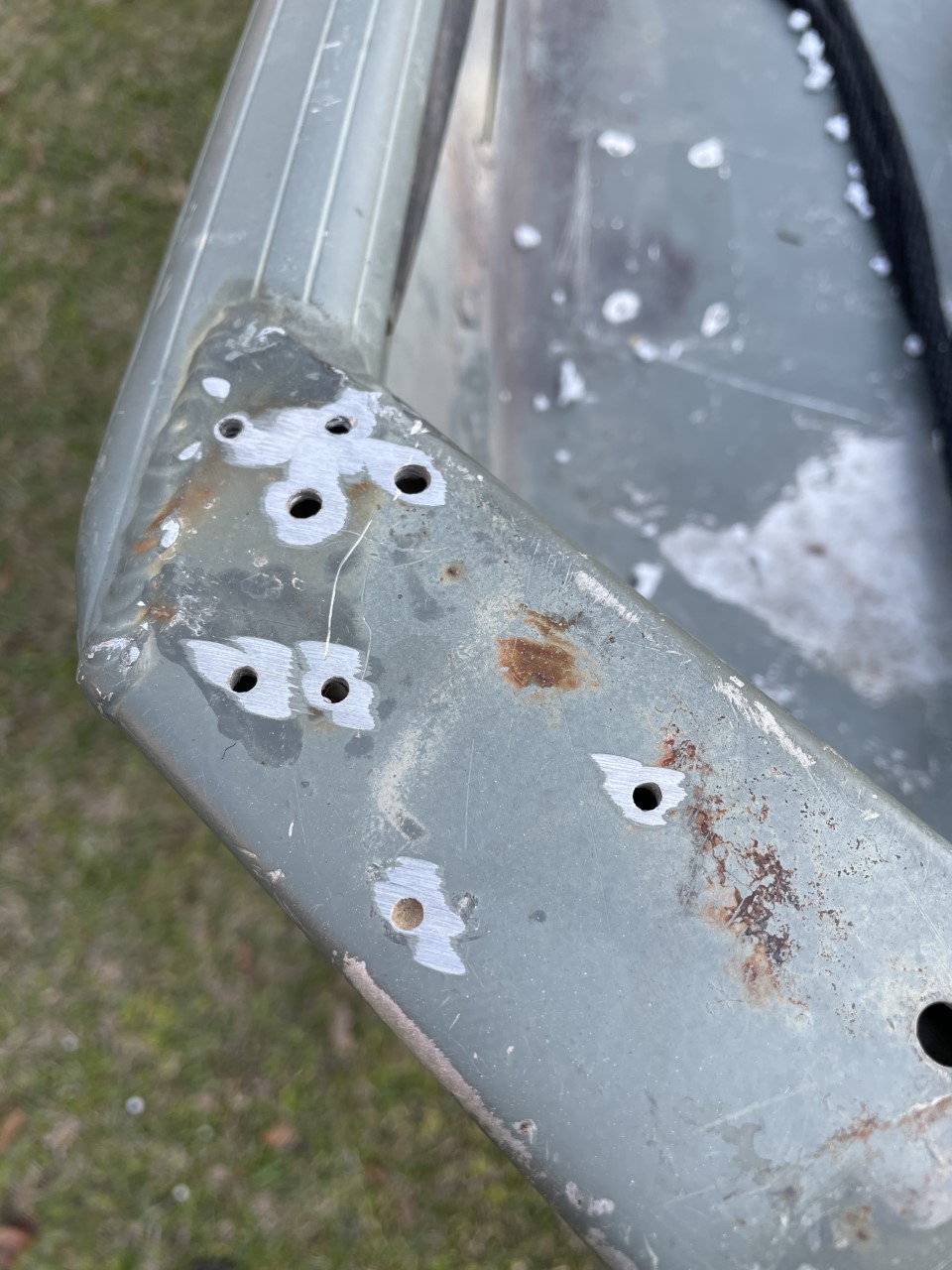
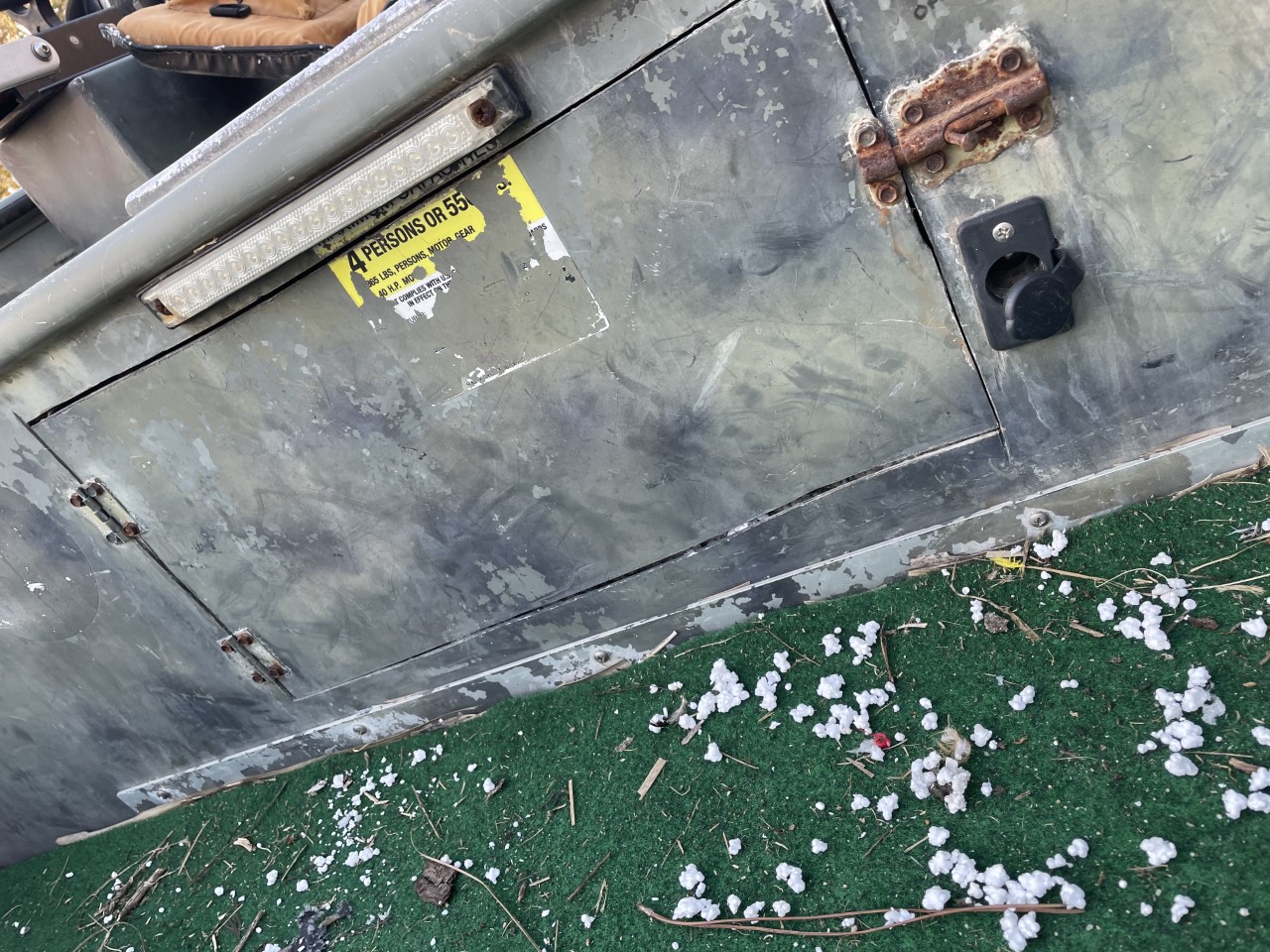
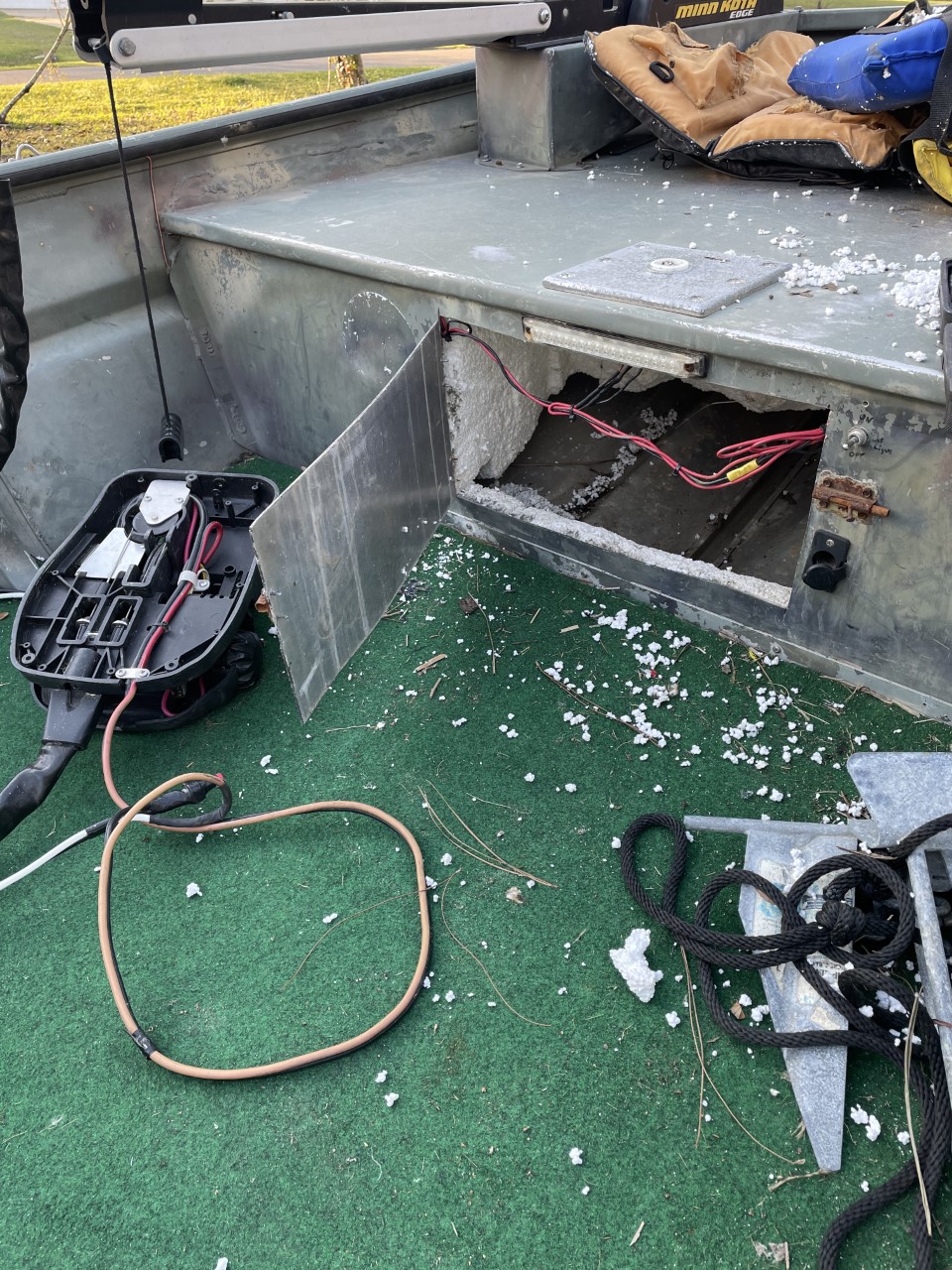
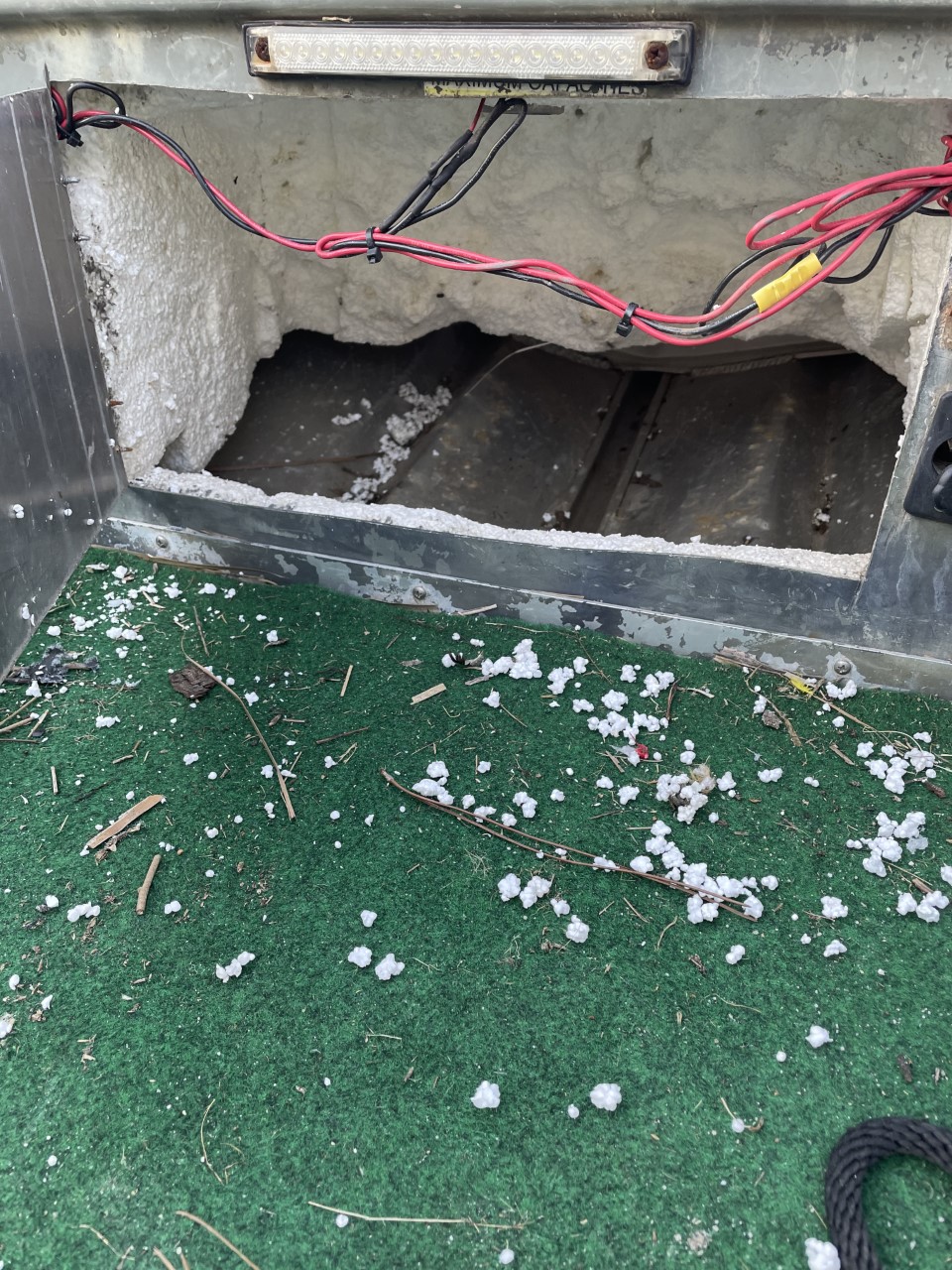
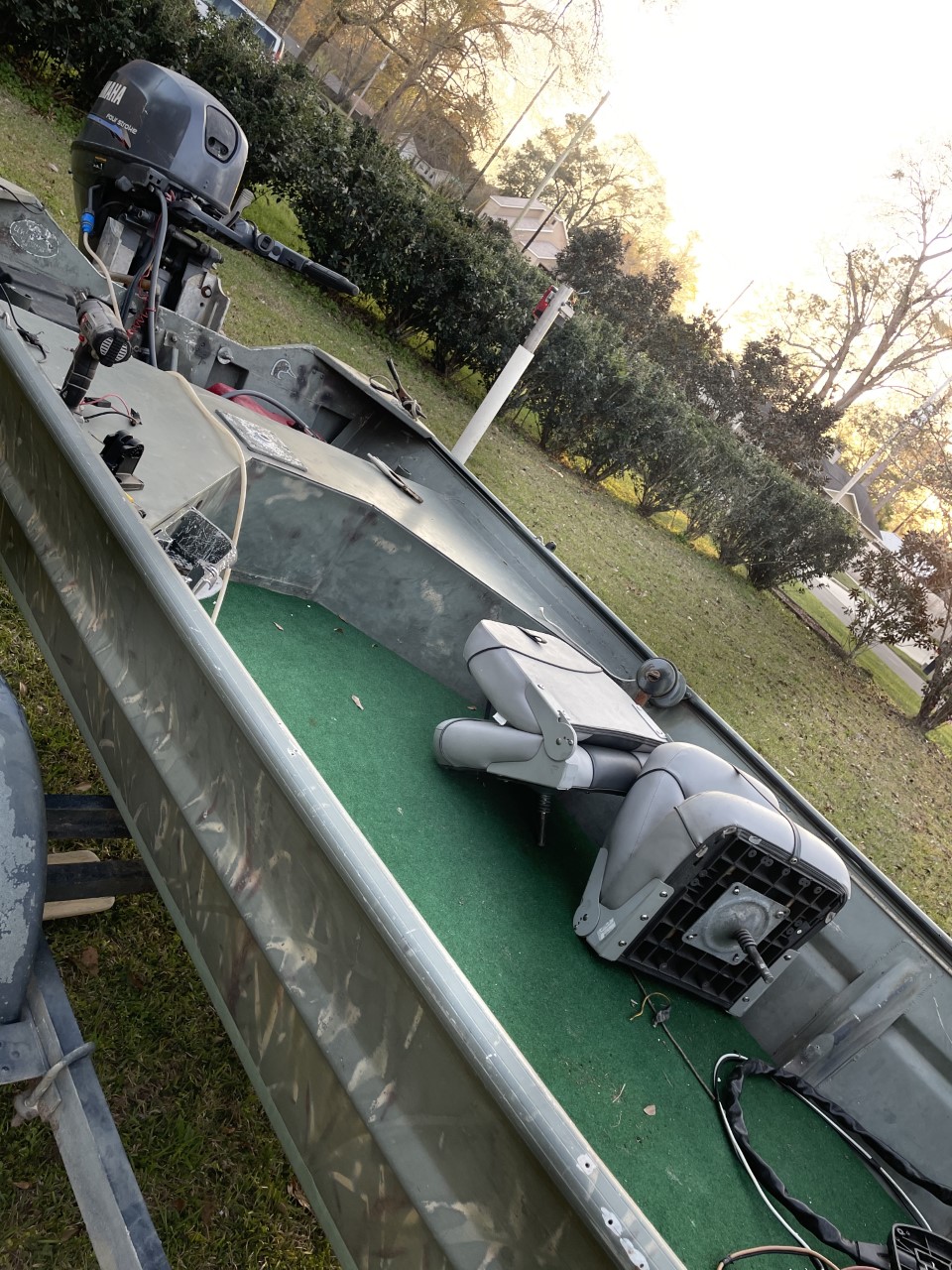