First time posting here. Lots of reading so far. Great inspiration on this forum.
I recently bought an old Valco Bayrunner hull to fix up. I got it knowing it was going to be a project. We go to Baja every year and the combination of the high bow and wide beam, while still being lightweight, is pretty near perfect for our use.
The previous owner(s) had done some work on the hull; none of it good. The seats and transom had been replaced but they'd been done with crap plywood, and unsealed at that. So naturally my first step was to take out the approximately 500 pounds of water-logged ply. Yuck. The good is that everything under all that looked pristine. Not a single cracked or broken weld forward of the transom.
The same guy(s) had also 'repaired' the transom. There had obviously been a corrosion issue - and the 'solution' was to weld another sheet of aluminum onto the outside of the transom skin. When I pulled the transom ply I found some pretty extensive corrosion on the inner (original) skin. The outer (new) skin appears to be in decent shape, at least from the outside. I think it's .125" plate. The interior is significantly thinner, I would guess .060" or .080".
I'm worried that there is corrosion and water trapped on the back side of the original skin and that'll eventually start eating the new one.
Not sure how to proceed from here. I'm pretty handy but I haven't done any work with aluminum and I don't weld.
Part of me says clean it up, spray it liberally with CorrosionX, put down a new sealed plywood transom, and call it good.
Another part of me wants to cut out all of the 'repair', then take it to one of the aluminum boatbuilders locally and have them put a proper transom on it. I don't know how much that might cost, but I'm doubting it's free.
Outside transom:
Inside after removal of ply and a bit of cleanup:
Worst spot of corrosion on interior:
Five or six spots of corrosion/pitting like this on interior. Holes are screw holes, not pits.
I recently bought an old Valco Bayrunner hull to fix up. I got it knowing it was going to be a project. We go to Baja every year and the combination of the high bow and wide beam, while still being lightweight, is pretty near perfect for our use.
The previous owner(s) had done some work on the hull; none of it good. The seats and transom had been replaced but they'd been done with crap plywood, and unsealed at that. So naturally my first step was to take out the approximately 500 pounds of water-logged ply. Yuck. The good is that everything under all that looked pristine. Not a single cracked or broken weld forward of the transom.
The same guy(s) had also 'repaired' the transom. There had obviously been a corrosion issue - and the 'solution' was to weld another sheet of aluminum onto the outside of the transom skin. When I pulled the transom ply I found some pretty extensive corrosion on the inner (original) skin. The outer (new) skin appears to be in decent shape, at least from the outside. I think it's .125" plate. The interior is significantly thinner, I would guess .060" or .080".
I'm worried that there is corrosion and water trapped on the back side of the original skin and that'll eventually start eating the new one.
Not sure how to proceed from here. I'm pretty handy but I haven't done any work with aluminum and I don't weld.
Part of me says clean it up, spray it liberally with CorrosionX, put down a new sealed plywood transom, and call it good.
Another part of me wants to cut out all of the 'repair', then take it to one of the aluminum boatbuilders locally and have them put a proper transom on it. I don't know how much that might cost, but I'm doubting it's free.
Outside transom:
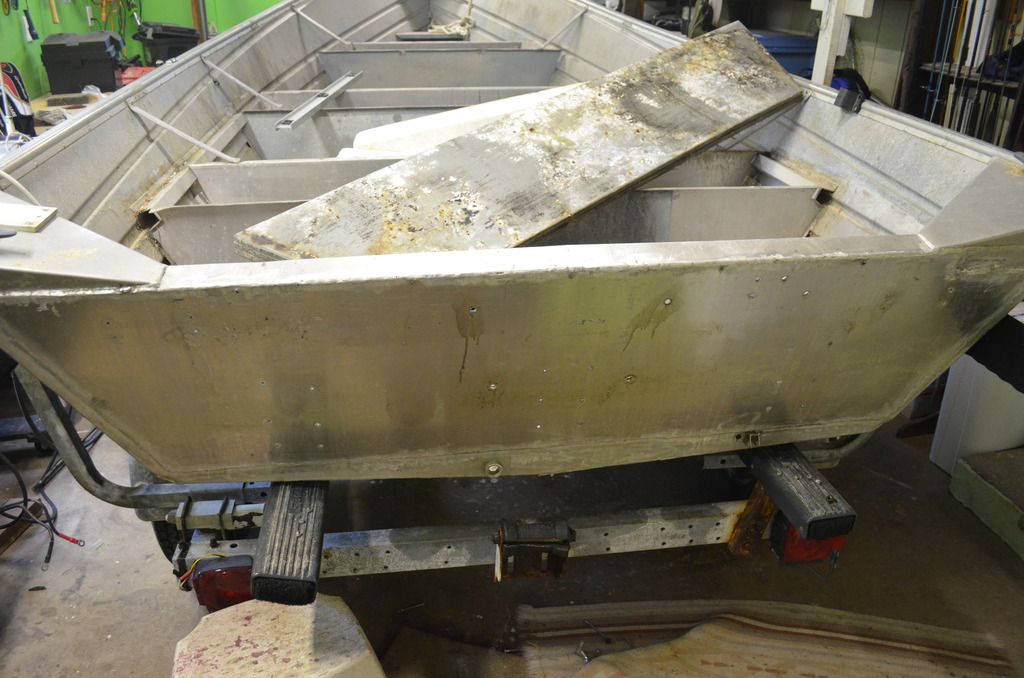
Inside after removal of ply and a bit of cleanup:
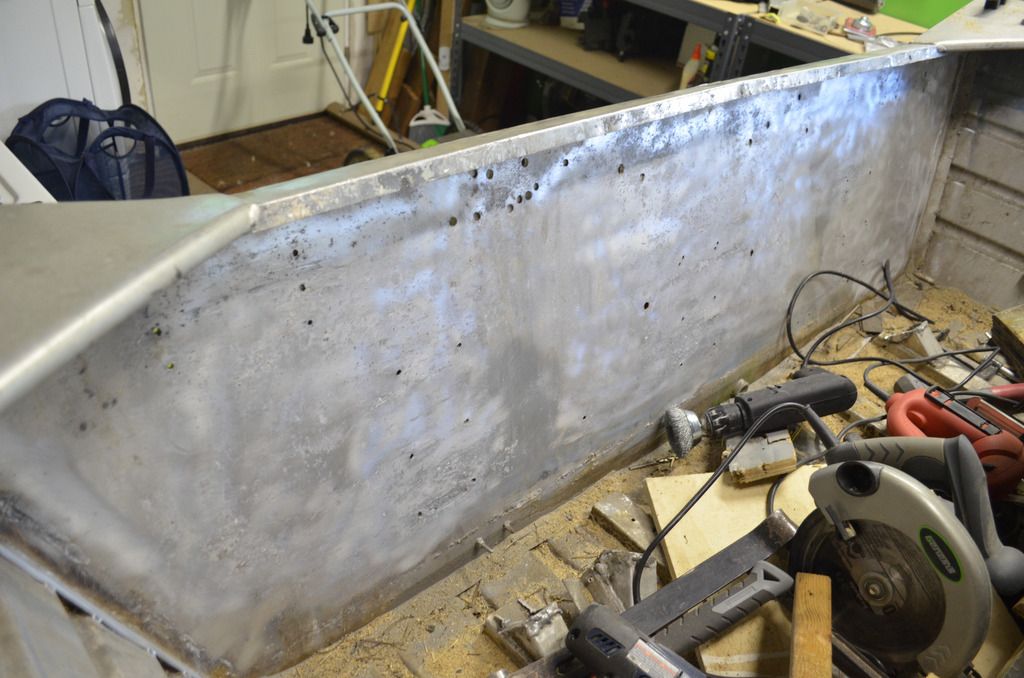
Worst spot of corrosion on interior:
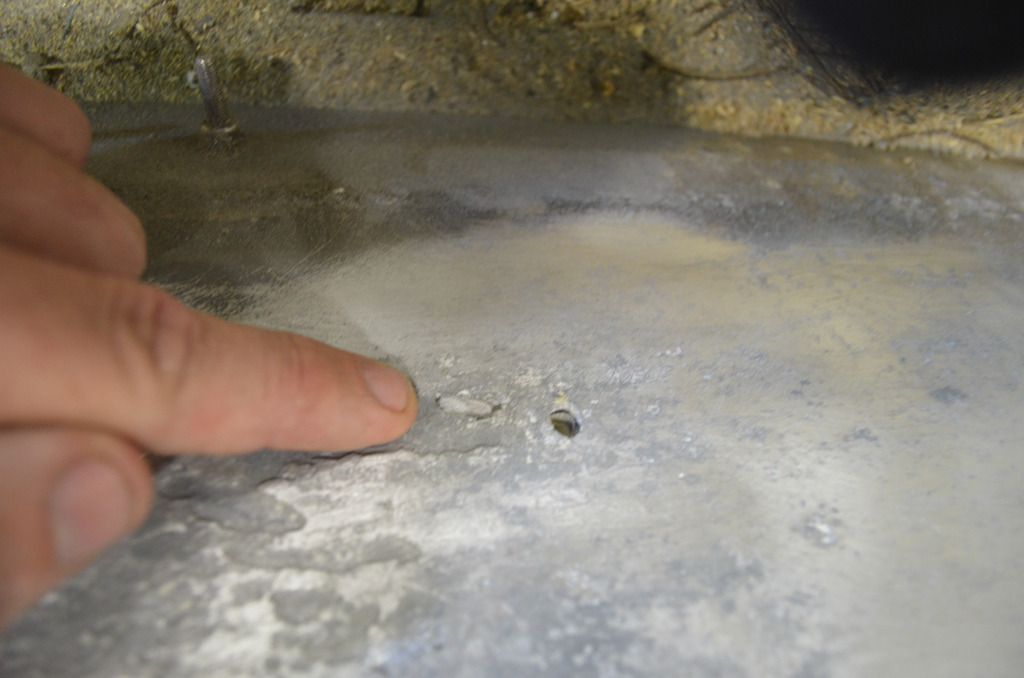
Five or six spots of corrosion/pitting like this on interior. Holes are screw holes, not pits.
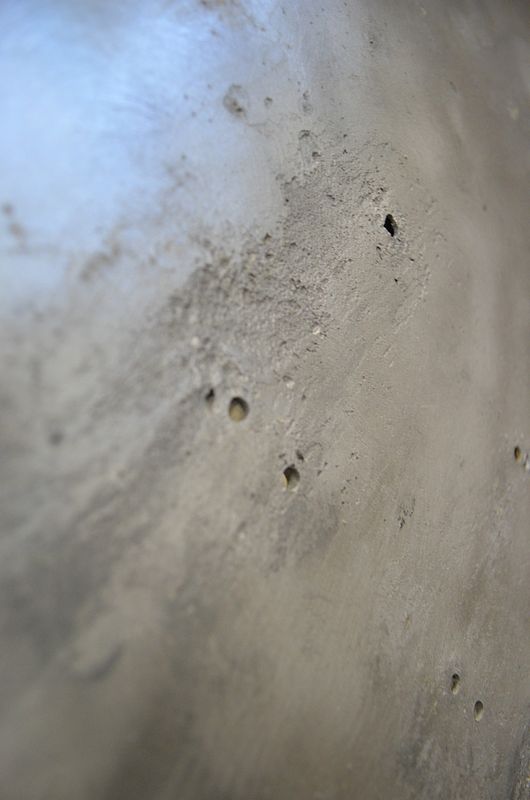