lbursell
Well-known member
Here At Last! Its painting day for the trailer frame. I had every thing laid out in the garage, then decided I didn't want to go to the trouble of turning the entire garage into a big paint booth.
So, I loaded every thing into the back of the truck for a trip to the carwash to get rid of any last bits of dirt or oil residue.
Back from the carwash and ready for primer. I had a low volume spray gun that I borrowed from my Dad to do the spraying with, but my little pancake compessor just didn't have enough "oomph" to do the job.
So, a quick trip to Wal-mart and I bought a Wagner Power Painter. More about that thing in a minute. This is the primer I used for the galvanized metal.
Every thing all primed and looking pretty good.
These are the saw-horses I used while spraying with the Wagner Painter. Notice the amount of overspray. There's also a huge spot of much lighter concrete on my driveway.
Sorry, but I've got to rant here. :evil: I will never, ever recommend the Wagner Power so-called Painter to anyone. If you don't hold it exactly level, it loses suction. Despite have everything set at the lowest possible volume, it still spewed out clumps of paint. No matter which nozzle setting I used, there was no way to avoid enormous overspray. With the amount of area I needed to paint, I should have been able to prime at least two trailers with the one can of primer. Instead, I had to use a full second and part of a third can to finish the job. When I was done, I completely cleaned the worthless piece of junk exactly according to the instructions and took it back to Wal-mart. Told them that they should be ashamed to sell that kind of stuff to the public. I figure they must have been used to hearing that, 'cause they refunded my money with no questions asked. As I posted on another thread, If you offered me a T-bone steak with the name "Wagner" on it, I'd rather go to McDonalds. And, I am no fan of that clown, either. I will never buy another Wagner product again.
OK, its out of my system; Rant over. 8)
While the primer was drying, I decided to paint the trailer guide-ons.
The guide-ons got Krylon Fusion paint for plastic and PVC.
Redneck paint booth in action.
All the frame parts back in the garage, ready for top coat. After my adventures with the sprayers, I decided that low tech rollers were my best route.
Valspar Tractor/Farm Implement Paint from Tractor Supply. The little trigger attachment for the spray cans is great. Makes using the cans so very easy. I used the spray cans for the little nooks and crannies that the rollers couldn't get into.
And the pay-off.
A little re-assembley and tires, wheels, fenders and frame all coming together. This is why we do it.
I like this blue. The boat and the trailer are going to be the same color. This is a sample of the HydroTurf mat that the decking will be covered with. I'm gonna try the HydroTurf instead of carpet. I think the blues match each other pretty good.
Next up, bunks and bunk carpetting.
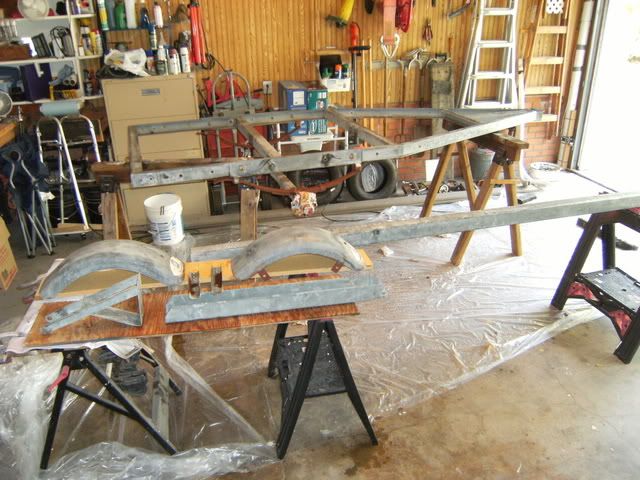
So, I loaded every thing into the back of the truck for a trip to the carwash to get rid of any last bits of dirt or oil residue.
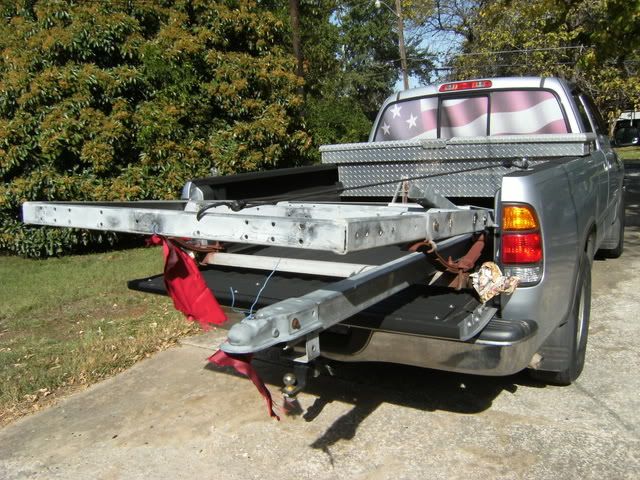
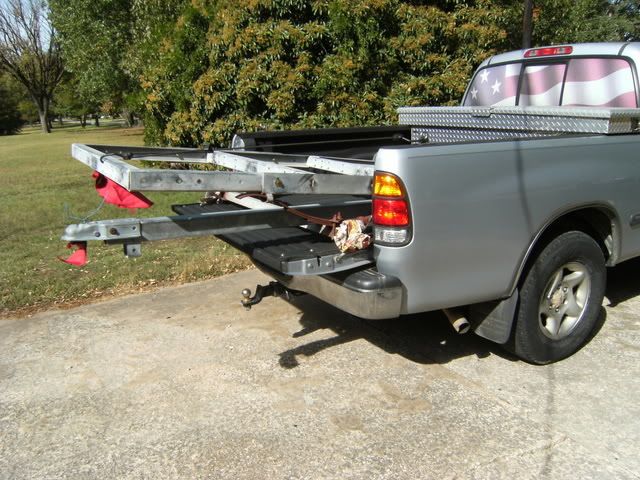
Back from the carwash and ready for primer. I had a low volume spray gun that I borrowed from my Dad to do the spraying with, but my little pancake compessor just didn't have enough "oomph" to do the job.
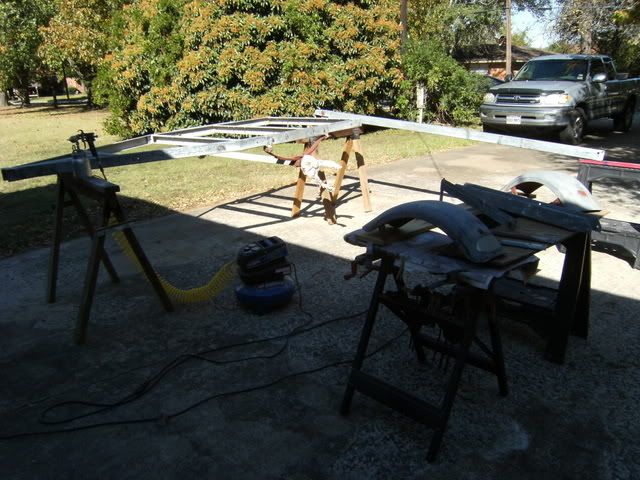
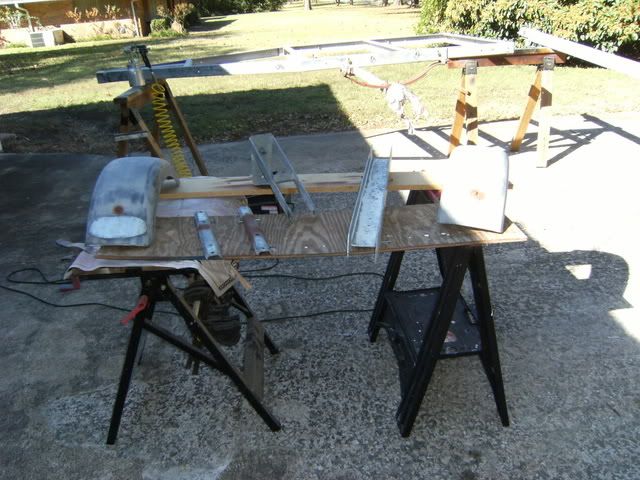
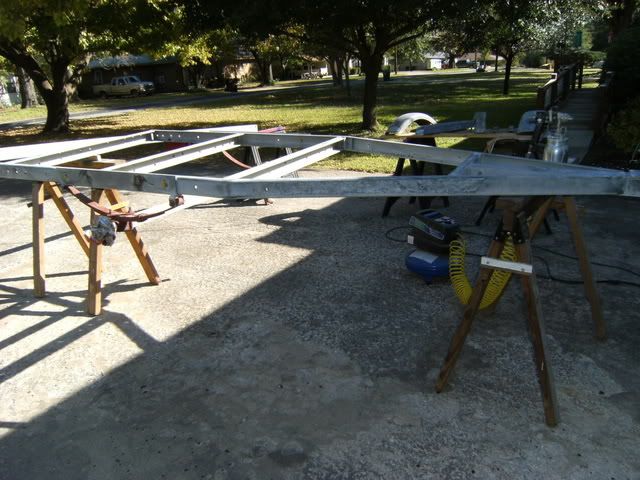
So, a quick trip to Wal-mart and I bought a Wagner Power Painter. More about that thing in a minute. This is the primer I used for the galvanized metal.
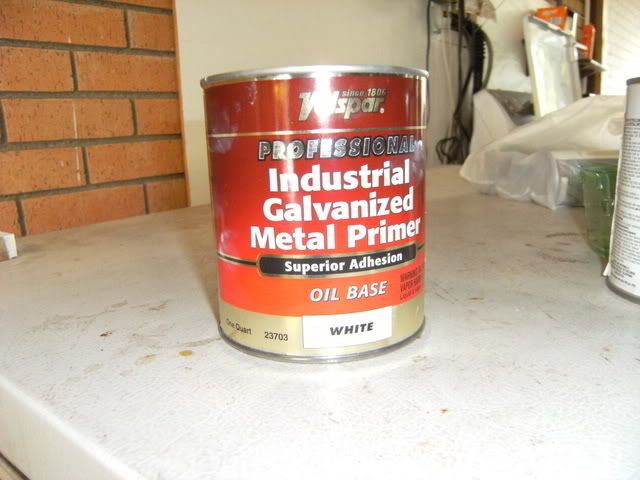
Every thing all primed and looking pretty good.
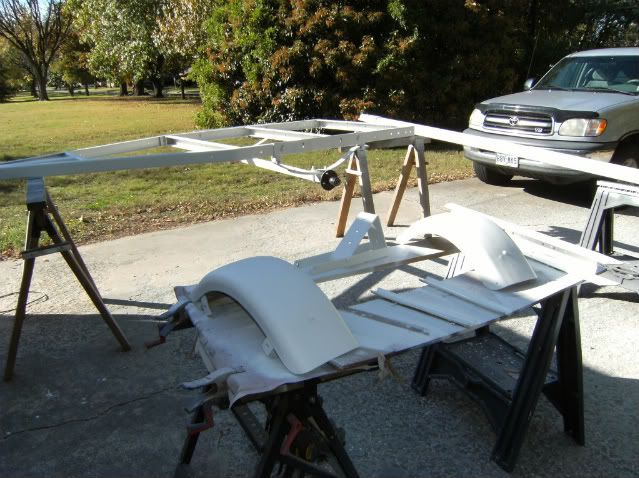
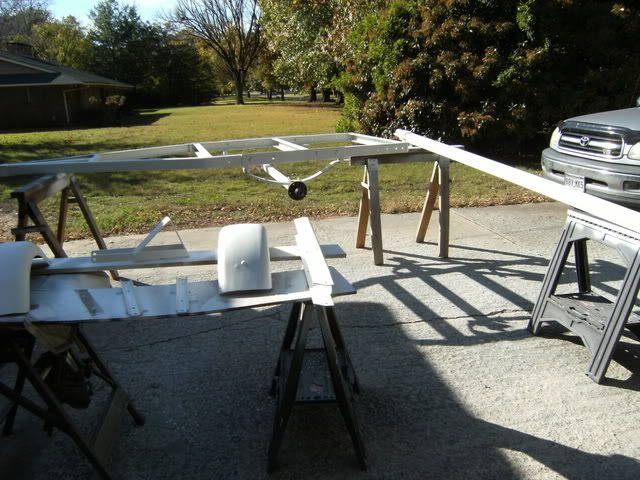
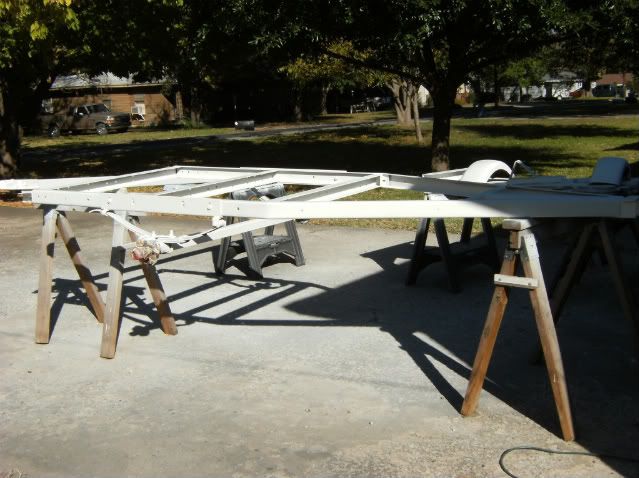
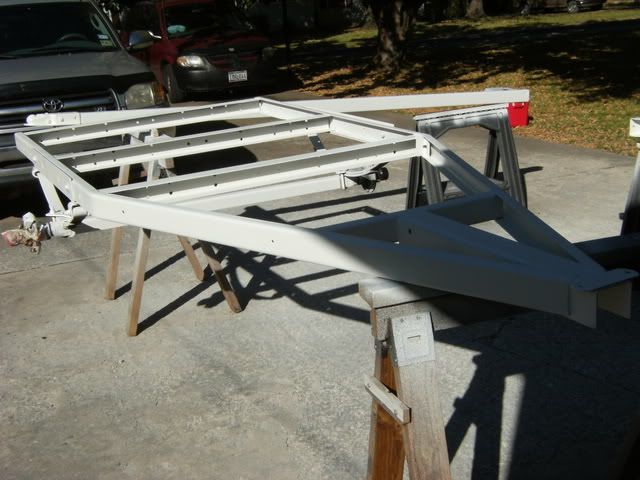
These are the saw-horses I used while spraying with the Wagner Painter. Notice the amount of overspray. There's also a huge spot of much lighter concrete on my driveway.
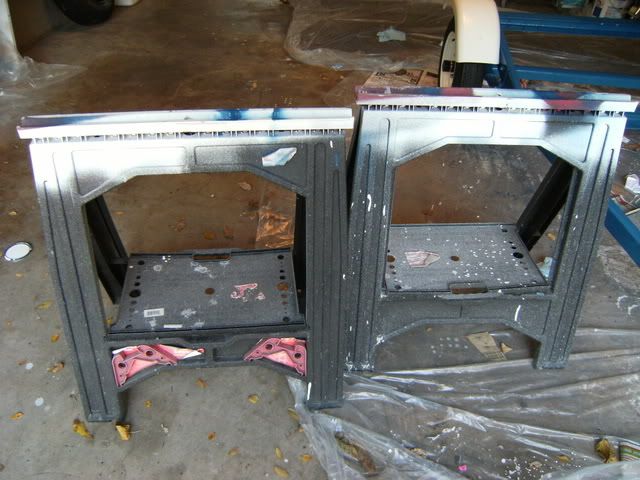
Sorry, but I've got to rant here. :evil: I will never, ever recommend the Wagner Power so-called Painter to anyone. If you don't hold it exactly level, it loses suction. Despite have everything set at the lowest possible volume, it still spewed out clumps of paint. No matter which nozzle setting I used, there was no way to avoid enormous overspray. With the amount of area I needed to paint, I should have been able to prime at least two trailers with the one can of primer. Instead, I had to use a full second and part of a third can to finish the job. When I was done, I completely cleaned the worthless piece of junk exactly according to the instructions and took it back to Wal-mart. Told them that they should be ashamed to sell that kind of stuff to the public. I figure they must have been used to hearing that, 'cause they refunded my money with no questions asked. As I posted on another thread, If you offered me a T-bone steak with the name "Wagner" on it, I'd rather go to McDonalds. And, I am no fan of that clown, either. I will never buy another Wagner product again.
OK, its out of my system; Rant over. 8)
While the primer was drying, I decided to paint the trailer guide-ons.
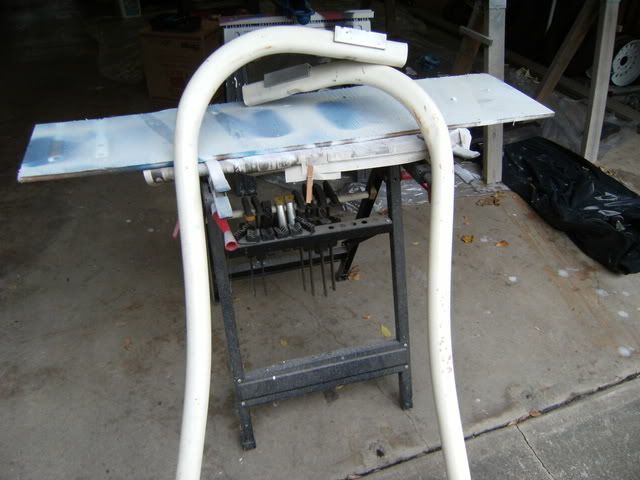
The guide-ons got Krylon Fusion paint for plastic and PVC.
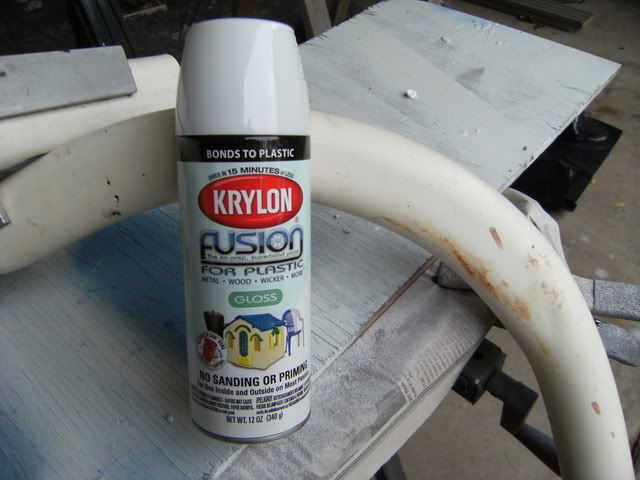
Redneck paint booth in action.
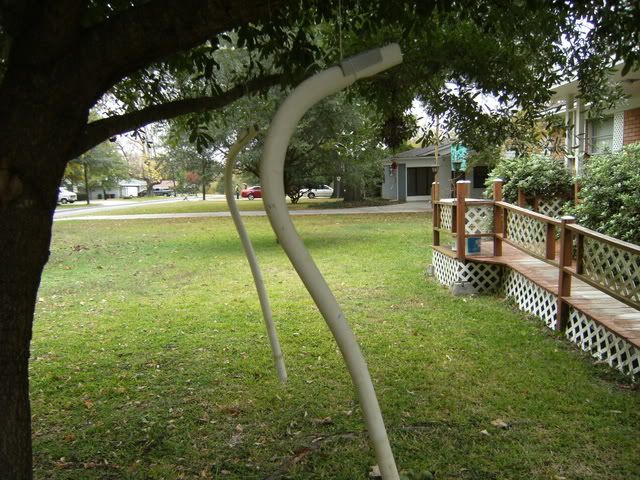
All the frame parts back in the garage, ready for top coat. After my adventures with the sprayers, I decided that low tech rollers were my best route.
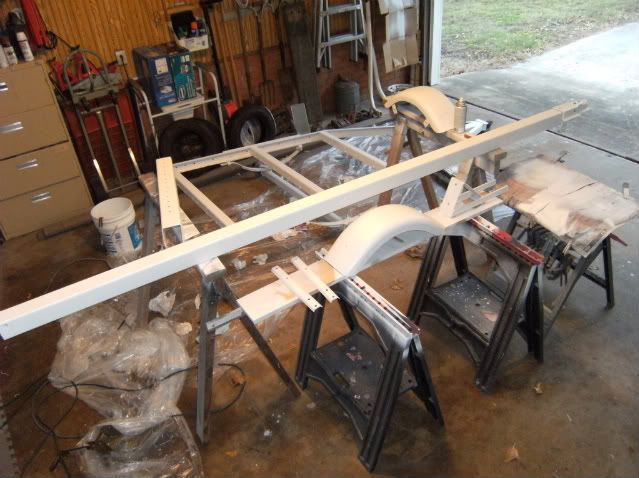
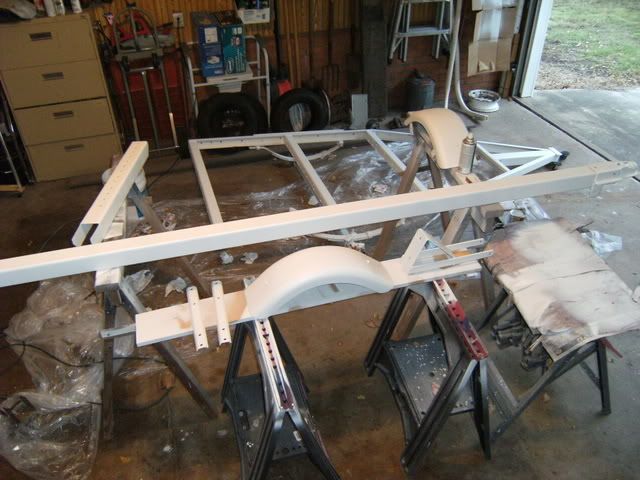
Valspar Tractor/Farm Implement Paint from Tractor Supply. The little trigger attachment for the spray cans is great. Makes using the cans so very easy. I used the spray cans for the little nooks and crannies that the rollers couldn't get into.
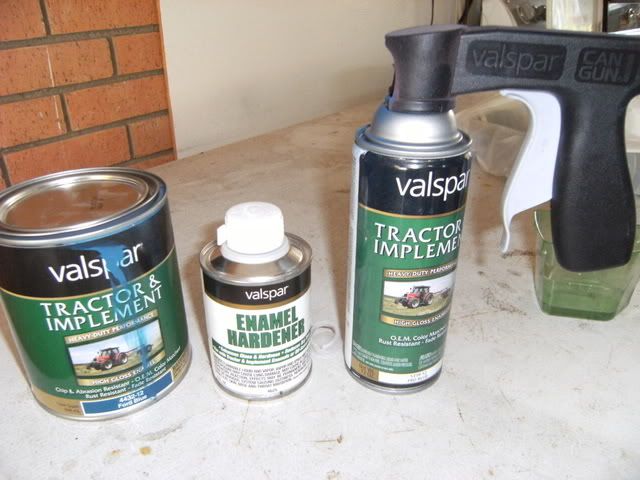
And the pay-off.
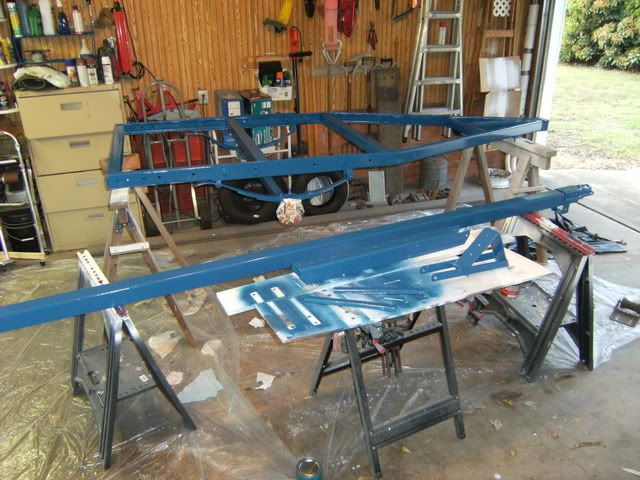
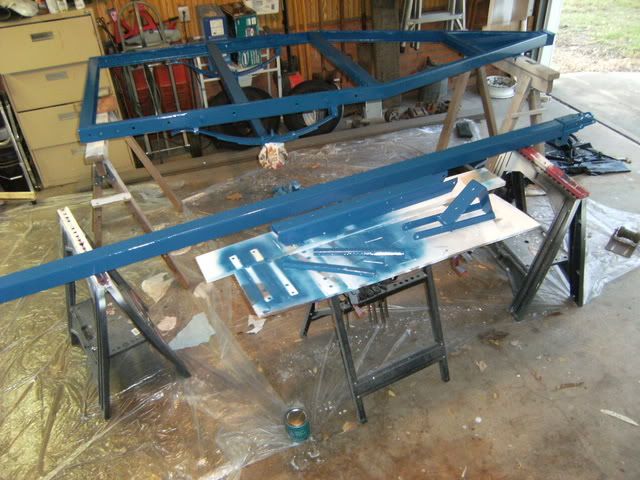
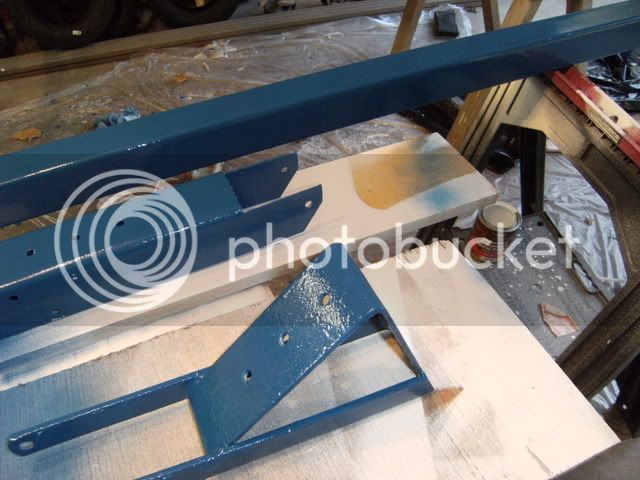
A little re-assembley and tires, wheels, fenders and frame all coming together. This is why we do it.
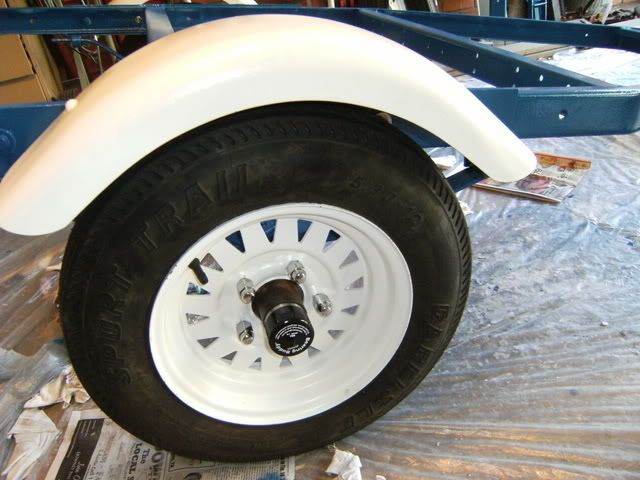
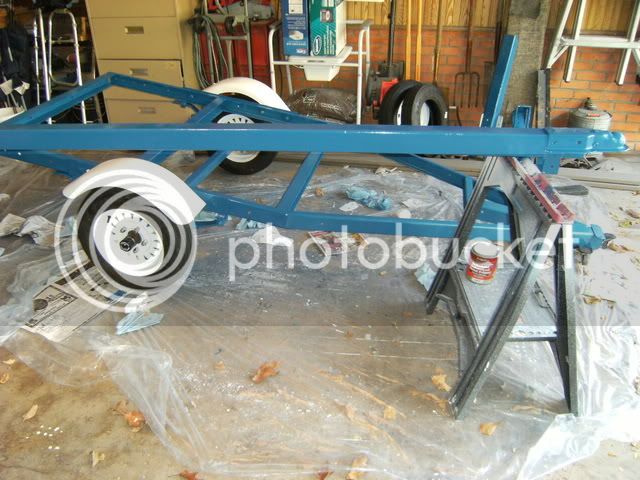
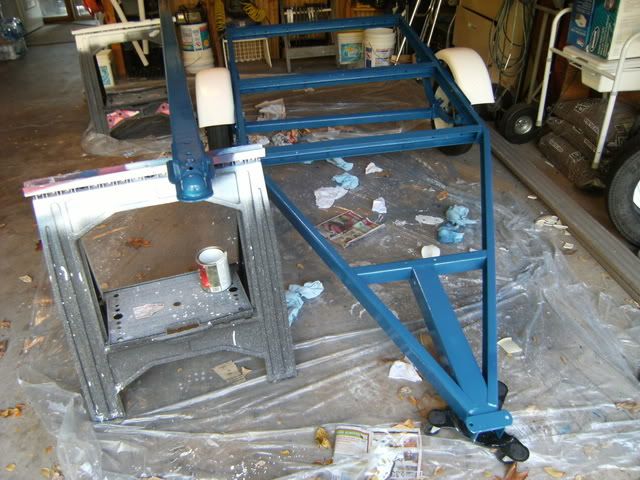
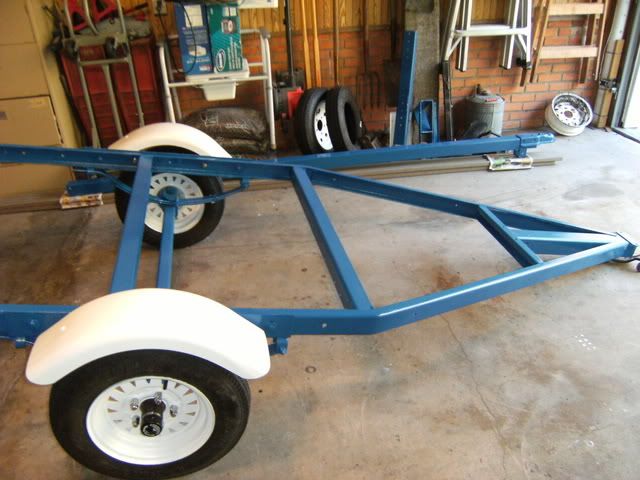
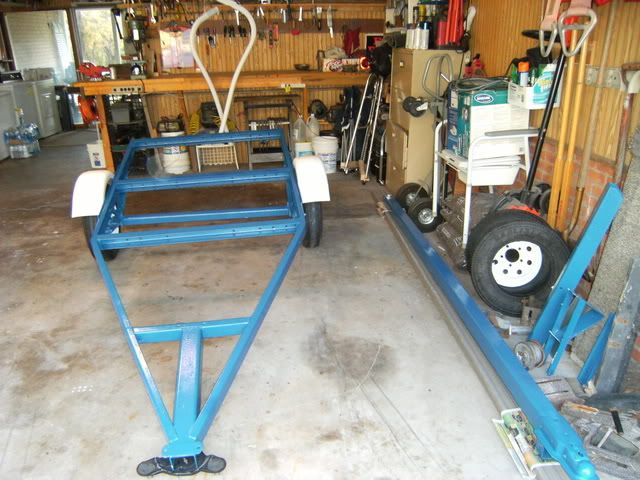
I like this blue. The boat and the trailer are going to be the same color. This is a sample of the HydroTurf mat that the decking will be covered with. I'm gonna try the HydroTurf instead of carpet. I think the blues match each other pretty good.
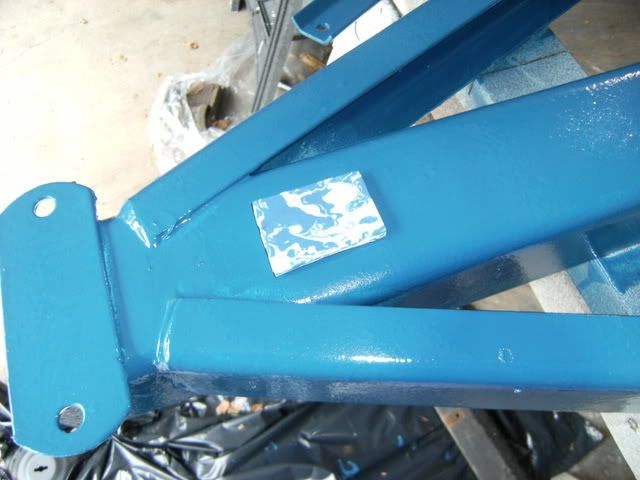
Next up, bunks and bunk carpetting.