onthewater102
Well-known member
Picked up an old Tracker III and found an '88 Mercury 60hp 2 stroke to ride on the back. Learned a lot on my 1436 Alumacraft build, so wherever possible I'll be using solid rivets for joining the aluminum support angles together and any poured foam that goes in will not be allowed to block the drain channels stamped in the bottom of the boat.
Plan is to gut everything and install a rod locker running from the bow to under the steering wheel along with a larger front deck with lockable storage compartments. I'll be replacing the bench with a setup allowing for more storage beneath the bench seating area along with a folding extension for the rear deck which will cover the bench when not in use. Trying to maximize the amount of lockable storage space available while also adding more elevated surface areas. The inaccessible spaces will for the most part be filled with expanding foam, but each compartment will first have the drainage channels capped in FRP and then be lined with painter's plastic prior to pouring foam, the goal of which is threefold:
1) none of the drainage channels will be blocked
2) the foam will formed to the cavity but not be bonded to the boat hull making it removable
3) the plastic should form a vapor barrier so the foam will not be in direct contact with any drainage waters
My plan starting out is to cap the bow and have a hatch to allow access to the storage space and wiring (trolling motor & nav lights) underneath. Framing this looks to be a bit tricky with the round gunwales. I will be using aluminum sheeting for all the decking surfaces. The final finish will not be carpet, though going in I'm torn between a textured paint and marine vinyl, the jury will have to wait to decide on that later. I'll be sharing the trolling motor and fishfinder electronics between this rig and my 14'. As much as I'd like to make this a center console I won't have room for both the rod locker and the storage boxes I want if I use this configuration, so it'll be staying a side steering setup. Hoping to add a 3rd seat base for trips with both my kids. It'll be a tight squeeze in what is basically a 1648 but we'll make it work.
I got ahead of myself on the tear down and already had the steering wheel out before I remembered to take a before picture, so this is all I've got:
It was in OK shape, the plywood decks were starting to show soft spots and the mild steel base for the bench seat left a lot to be desired. The original bench was not in a condition I considered to be worth trying to restore, it has a 1/2 dollar sized hole in one spot, all the seams are separating and the foam needs replacing, but if someone thinks otherwise they're welcome to it just send me a PM.
Gutting went well enough, I'm going to leave the original framing in I think and work around it.
Removed the foam from one of the compartments up front. Slicing through it with an old-school hand saw makes it easy to remove in chunks.
And one last shot of the emptied out compartment, still needed to clear the drain channel that was clogged with foam:
Made up 10 rod tubes for the front using the RichZ heat gun and wine bottle trick. Once flared on the wine bottle I heated themn a second time and pressed them down on a cold floor tile to make a flat flange. After test fitting an arrangement I think I'll be able to add 6 more rod tubes outside the starboard locker along the port side of the boat (3 running forward, 3 running aft-ward), so I'm going to have to get 3 more pieces of pipe as these were all cut in half to 5' lengths and I think the others will need to be cut unevenly (6' forward / 4' aft). Having room on board to store 16 rods below decks in a 16' boat will be awesome.
That's it for now - waiting on an 1 11/16 Forstner bit from amazon to drill the holes for the tubes through the existing support panel. In the mean time I'll get the rest of the old carpet adhesive removed, get the foam out on the port side and the rear quarter to allow me to install the extra 6 tubes and start framing everything.
Plan is to gut everything and install a rod locker running from the bow to under the steering wheel along with a larger front deck with lockable storage compartments. I'll be replacing the bench with a setup allowing for more storage beneath the bench seating area along with a folding extension for the rear deck which will cover the bench when not in use. Trying to maximize the amount of lockable storage space available while also adding more elevated surface areas. The inaccessible spaces will for the most part be filled with expanding foam, but each compartment will first have the drainage channels capped in FRP and then be lined with painter's plastic prior to pouring foam, the goal of which is threefold:
1) none of the drainage channels will be blocked
2) the foam will formed to the cavity but not be bonded to the boat hull making it removable
3) the plastic should form a vapor barrier so the foam will not be in direct contact with any drainage waters
My plan starting out is to cap the bow and have a hatch to allow access to the storage space and wiring (trolling motor & nav lights) underneath. Framing this looks to be a bit tricky with the round gunwales. I will be using aluminum sheeting for all the decking surfaces. The final finish will not be carpet, though going in I'm torn between a textured paint and marine vinyl, the jury will have to wait to decide on that later. I'll be sharing the trolling motor and fishfinder electronics between this rig and my 14'. As much as I'd like to make this a center console I won't have room for both the rod locker and the storage boxes I want if I use this configuration, so it'll be staying a side steering setup. Hoping to add a 3rd seat base for trips with both my kids. It'll be a tight squeeze in what is basically a 1648 but we'll make it work.
I got ahead of myself on the tear down and already had the steering wheel out before I remembered to take a before picture, so this is all I've got:
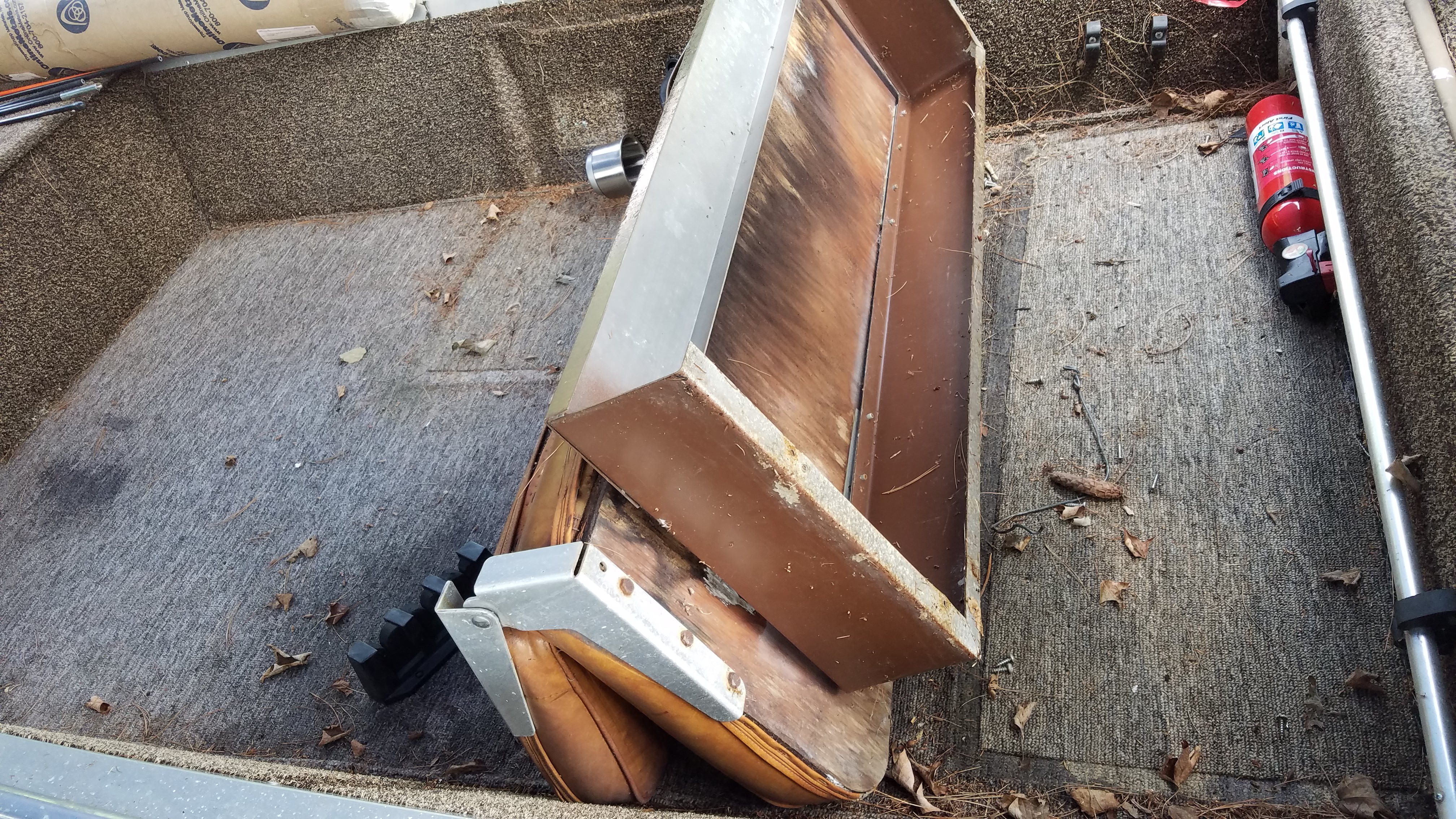
It was in OK shape, the plywood decks were starting to show soft spots and the mild steel base for the bench seat left a lot to be desired. The original bench was not in a condition I considered to be worth trying to restore, it has a 1/2 dollar sized hole in one spot, all the seams are separating and the foam needs replacing, but if someone thinks otherwise they're welcome to it just send me a PM.
Gutting went well enough, I'm going to leave the original framing in I think and work around it.
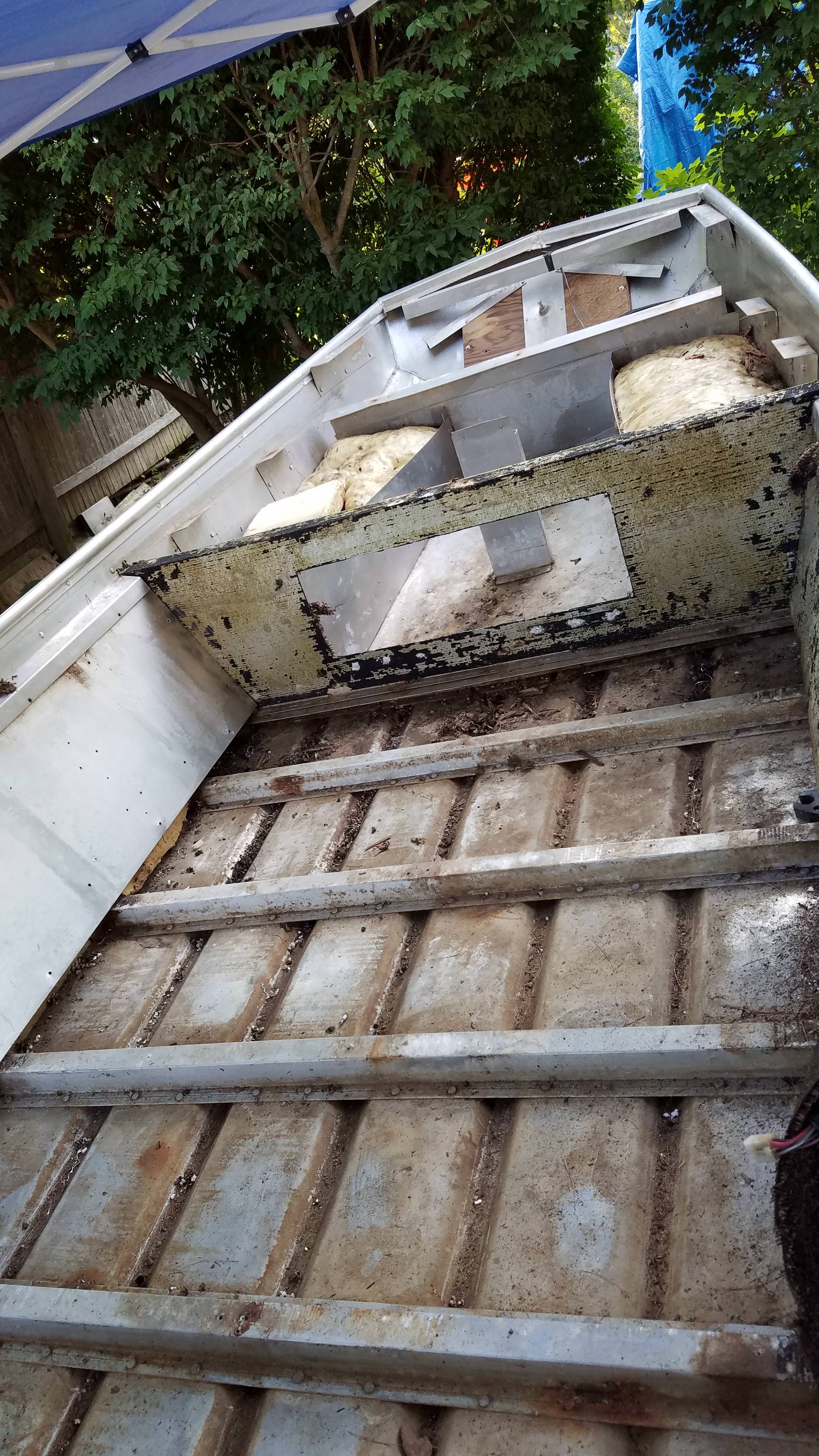
Removed the foam from one of the compartments up front. Slicing through it with an old-school hand saw makes it easy to remove in chunks.
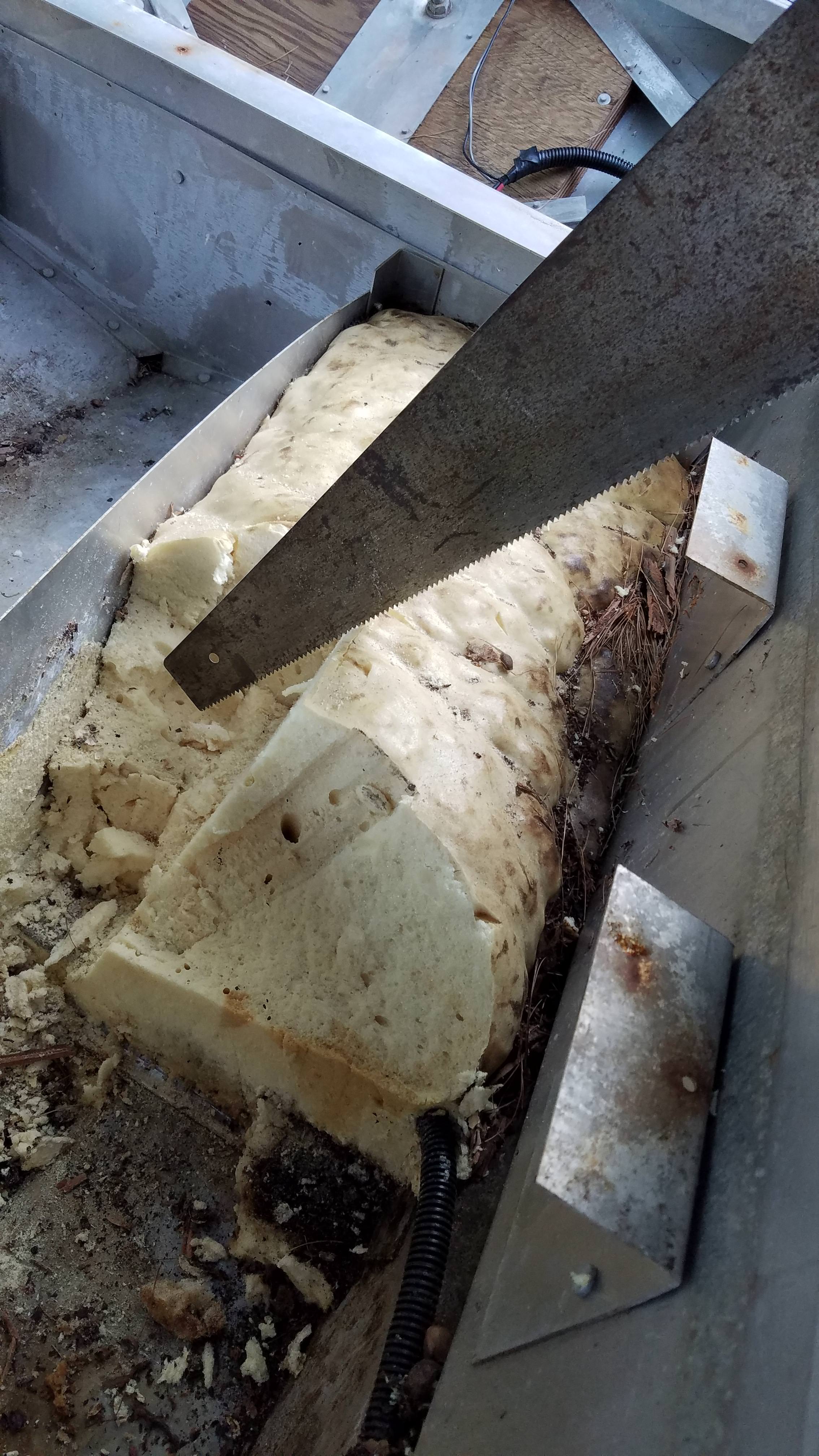
And one last shot of the emptied out compartment, still needed to clear the drain channel that was clogged with foam:
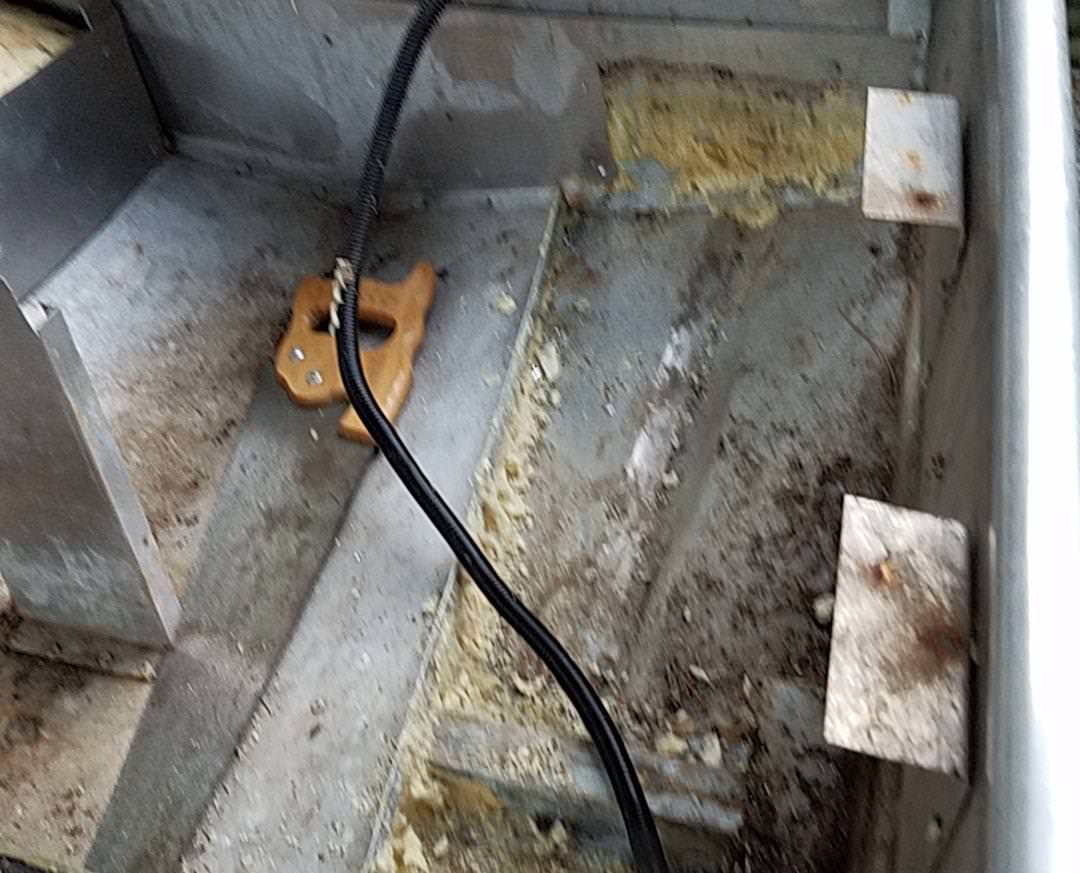
Made up 10 rod tubes for the front using the RichZ heat gun and wine bottle trick. Once flared on the wine bottle I heated themn a second time and pressed them down on a cold floor tile to make a flat flange. After test fitting an arrangement I think I'll be able to add 6 more rod tubes outside the starboard locker along the port side of the boat (3 running forward, 3 running aft-ward), so I'm going to have to get 3 more pieces of pipe as these were all cut in half to 5' lengths and I think the others will need to be cut unevenly (6' forward / 4' aft). Having room on board to store 16 rods below decks in a 16' boat will be awesome.
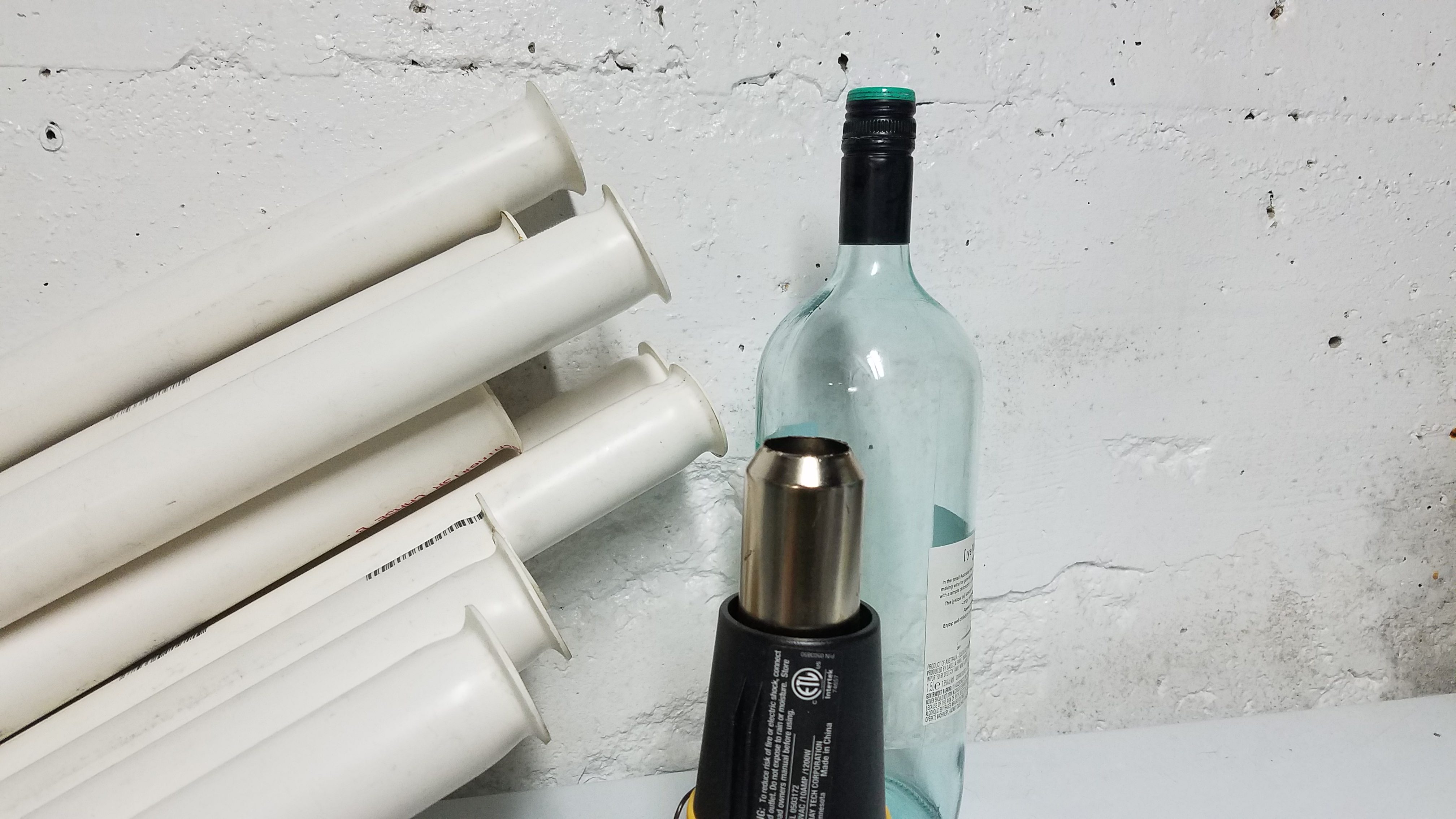
That's it for now - waiting on an 1 11/16 Forstner bit from amazon to drill the holes for the tubes through the existing support panel. In the mean time I'll get the rest of the old carpet adhesive removed, get the foam out on the port side and the rear quarter to allow me to install the extra 6 tubes and start framing everything.